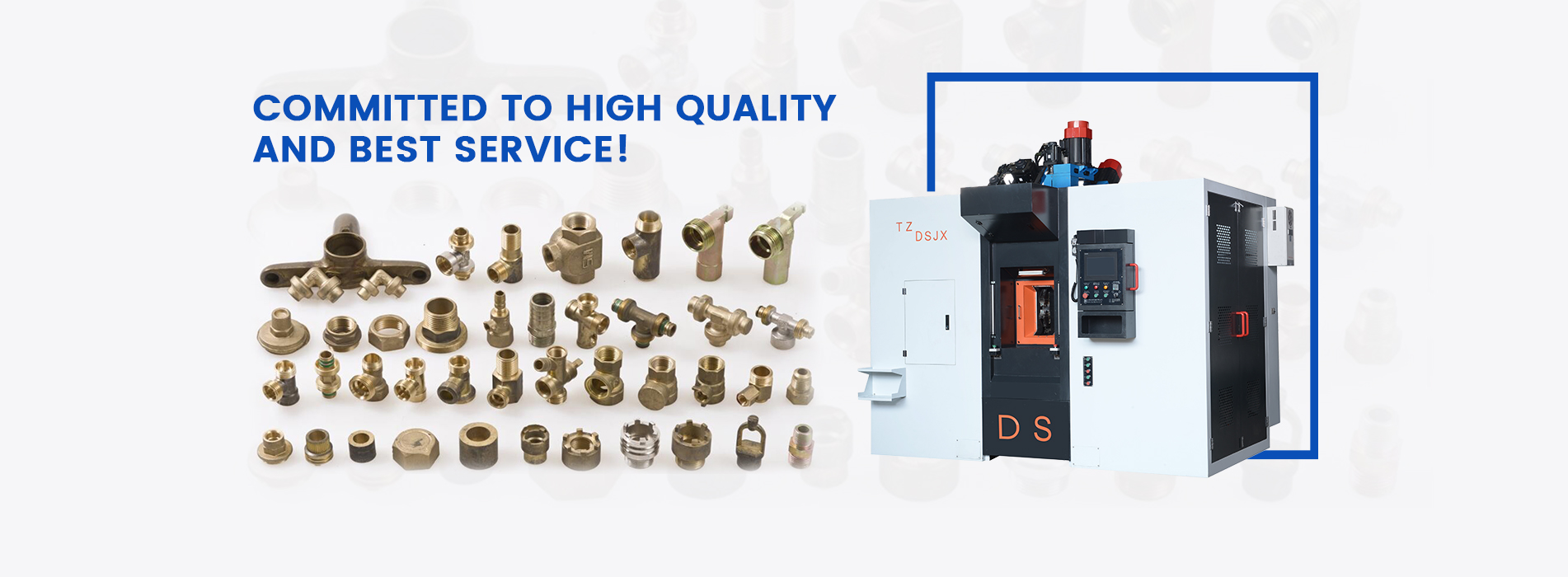
What is Gravity Casting: Gravity casting refers to the process of injecting molten metal into a mold under the action of the earth's gravity, also known as casting. The generalized gravity casting includes sand casting, metal casting, investment casting, lost foam casting, mud casting, etc. The narrow gravity casting refers specifically to metal casting. The molten metal is generally poured into the gate manually, and the product is obtained by filling the cavity, exhausting, cooling, and opening the mold by its own weight. The process flow is: smelting, casting filling, exhaust, cooling, mold opening, heat treatment, and metal processing. Die casting introduction: Pressure casting is divided into two types: high pressure casting and low pressure casting. High pressure casting is a casting method in which molten alloy liquid is poured into a press chamber, the cavity of a steel mold is filled at high speed, and the alloy liquid is solidified under pressure to form a casting. The main characteristics of high pressure die casting that distinguish it from other casting methods are high pressure and high speed. ①The molten metal fills the cavity under pressure, and crystallizes and solidifies under higher pressure, the common pressure is 15-100MPa. ②The molten metal fills the cavity at a high speed, usually 10-50 m/s, and some can exceed 80 m/s, (the linear velocity of the cavity through the inner gate-the inner gate speed), so the molten metal The filling time is extremely short, and the cavity can be filled within about 0.01-0.2 seconds (depending on the size of the casting). The process of low-pressure casting is as follows: in a sealed crucible (or sealed tank), dry compressed air is introduced, and under the action of gas pressure, the molten metal enters the sprue along the riser pipe and rises smoothly through the inner runner. Enter the cavity and maintain the gas pressure on the liquid surface in the crucible. Until the casting is completely solidified. Then the gas pressure on the liquid surface is released, and the unsolidified molten metal in the riser pipe flows back to the crucible. Reopen the mold and take out the casting. It can also be said that low-pressure casting is a compromise between high-pressure casting and gravity casting. - https://www.desuautomatic.com/
The water supply system required for equipment testing consists of a hot water system and a cold water system, both of which usehigh-performance water pumps, andlt adopts fully automatic frequency conversion control, only need to manually set the water pressure value on the man-machine interface and turn on the water pump switch. Among them, the refrigeration system has two functions of cooling and auxiliary heating. When the temperature is high, the refrigeration is turned on, and vice versa. , Turn on auxiliary heat (auxiliary heat when the water temperature is low in winter). 1. The heating system provides the hot water temperature required for the test, and the refrigeration system provides the cold water temperature required for the test. The cold and hot water temperatures can be easily set and are automatically controlled by a thermocouple and PLC. The temperature control accuracy can reach ±2°C; 2. The cold water pump water supply system provides the cold water pressure required for the test, and the hot water pump water supply system provides the hot water pressure required for the test. Both the cold and hot water pressures are controlled by constant pressure frequency conversion. The closed-loop control principle is adopted and 0.5 is installed in the pressure test pipeline. The high-precision pressure sensor detects the pipeline pressure value in real time, and converts it into a 4-20mA signal and transmits it to the PLC signal acquisition module. The PLC outputs the corresponding signal to the frequency conversion according to the preset program and the pressure value set by the touch screen. Through the conversion of the output frequency of the inverter, the control of the constant pressure value of the output water pressure of the pressure water pump is realized: 3. The cold and hot supply and return water valve system is controlled by the PLC system. Through the touch screen parameter setting and the PLC built-in program, the alternate supply function of cold and hot water to the test sample can be realized, and the cold and hot water can be recovered separately. The circulating water can be reused after reheating or cooling to achieve the purpose of water saving and energy saving; 4. Drive device: The pressure used in the life test is automatically controlled by an air cylinder, and the drive head is equipped with soft materials to ensure that the pressing surface of the test sample is in flexible contact, and the effect of protecting the product is obtained; 5. Tooling and fixture: use the standard water tank required by JC987-2005: 400X175X300 (mm), the water tank has a hole inside, and the size of the hole can be changed to facilitate the realization of the joint, and obtain products of different specifications within the requirements of the test standard; 6. The electronic control system adopts PLC and touch screen, which can set the total test times, the test ratio of large/small gears, the pressing hold time, the stop water...
The difference between sand blasting machine and shot blasting 1. The working principle is different: Shot blasting uses a high-speed rotating impeller to throw small steel shots or small iron shots out to hit the surface of the part at high speed, so the oxide layer on the surface of the part can be removed. Sandblasting is a method of using compressed air to blow out the quartz sand at high speed to clean the surface of the part. 2.Different materials used The steel shots and iron shots used in shot blasting are not actually shots. To be precise, they are small steel wires or small steel rods. They only look like shots after a period of use. The so-called sandblasted sand is just river sand, which is no different from that used for construction, except that the sandblasted sand is screened, contains less mud, and has a particle size specification. Of course, some industries are also different. For example, real steel shot is used for shot blasting in the shipbuilding industry, and metal ore (not river sand-quartz sand) is used for sand blasting. 3. Different functions: The main function of sandblasting is to remove rust and scale on the surface, such as parts after heat treatment. Shot blasting has many functions. It not only removes rust and surface oxides, but also improves surface roughness, removes machining burrs of parts, eliminates internal stress of parts, reduces deformation of parts after heat treatment, and improves surface wear resistance of parts. Pressure capacity, etc. 4. Different materials used: The steel shots and iron shots used in shot blasting are not actually shots. To be precise, they are small steel wires or small steel rods. They only look like shots after a period of use. The so-called sandblasted sand is just river sand, which is no different from that used for construction, except that the sandblasted sand is screened, contains less mud, and has a particle size specification. Of course, some industries are also different. For example, real steel shot is used for shot blasting in the shipbuilding industry, and metal ore (not river sand-quartz sand) is used for sand blasting.
1. The fuselage is a solid hollow frame work piece. The upper part supports the indenter part of the rotating arm. When pressing, the rotating arm hooks the fuselage so that the pressing force is absorbed by the fuselage. The fuselage and the shock mechanism are bolted together, and the rotating arm In the indenter part, the indenter is fixed on a rocker arm that can be rotated, and the indenter has a screw elevator that can be adjusted to the distance from the indenter to the sand box according to the height of the sand box 2. The swing arm controls the reciprocating movement of the cylinder piston through a hand-pulled valve to realize the movement of the positive arm and swing arm. 3. The ejection structure is composed of two ejection cylinders, connecting rods, balance shafts, ejection tables, ejection rods, etc. When the ejection cylinders are activated, the connecting rods, balance shafts, and ejection tables are driven to eject the four ejector rods at the same time. Moulding from the sand box. 4. Shock compaction structure. Adopt spring micro-vibration pneumatic compaction structure, compaction shock increases vibration. The clamping cylinder locks the vibrating cylinder when the mold is drawn, and the clamping cylinder is released when the mold is dropped. 5. Pneumatic piping system: the input compressed air is removed by air filter to remove water and impurities in the compressed air, and then lubricating oil is injected through the lubricator to supply various pneumatic components and mechanisms, and the action of the machine is realized by the hand valve console . 6. Air supply and lubrication. The machine is operated by air source as energy source and oil as lubrication. The intake pressure and oil volume are respectively adjusted by the pressure reducing valve and the oil regulating valve. When the air source passes through the lubricator, the oil is sucked into the pipeline according to the siphon principle, and the mist enters the pipeline system for lubrication.
Fire sprinklers are used in fire sprinkler systems. When a fire occurs, water is sprinkled through the sprinkler splash plate to extinguish the fire. Currently, it is divided into pendant sprinklers, upright sprinklers, ordinary sprinklers, and side wall types. Sprinklers, etc. According to the definition in GB5135.1.3.1, sprinklers are: under the action of heat, they start automatically within a predetermined temperature range, or start by a control device according to a fire signal, and sprinkle water according to the designed sprinkler shape and flow rate. Water device. The automatic control fire sprinkler system is a fire extinguishing facility that can automatically turn on the sprinklers to sprinkle water and send out a fire alarm signal at the same time when a fire occurs. The automatic sprinkler extinguishing system has the advantages of automatic water spray, automatic alarm and initial fire cooling, etc., and can work in synchronization with other fire fighting facilities, so it can effectively control and extinguish the initial fire. It has been widely used in building fire protection. D&S Automatic Machine focuses on the production and research and development of red punching machines, which can be used to produce high-quality fire sprinklers. For more details, please contact D&S.
The automatic cutting machine has the following characteristics 1. The mechanical main circuit of the automatic cutting machine adopts Taiwan imported PLC control work, which is centralized and simple, sensitive, and convenient for maintenance; 2. Automatic feeding, non-stop feeding adopts Taiwan "Tec" servo Motor. Precision screw, cutting accuracy reaches ±0.03mm; 3.The counter can be set to process the number, or automatically stop, or accumulate the workload of the day; 4. The front and back pressure can be adjusted steplessly to ensure that the workpiece is not pinched and deformed; 5. When the processing size is changed, there is no need to manually locate the hardware, just change the relevant size data on the text display to work; 6. It has a significant effect on aluminum, copper, organic materials, plastic steel materials, carbon fiber, etc., cutting without burrs, The scraps after cutting are collected centrally, and the coolant can be recycled, which has the characteristics of high efficiency, time-saving and material-saving.
The automatic polishing machine realizes automatic surface polishing treatment, which is suitable for small workpieces and metal workpieces to automatically polish the surface gloss and remove burrs. One person can operate multiple devices. It is mainly used by customer groups such as handicraft processing plants, hardware processing plants, bathroom processing plants, and electronic processing plants. This type of equipment is relatively simple to operate and requires low operator skills, which can improve production efficiency, reduce labor intensity, save production costs, improve product quality, and reduce product quality differences. Remove burrs on the finished product; Surface rust treatment; Polish the surface of the finished product; Grinding and cleaning work; Clear the surface of the finished product Remove the oxide film (it will not damage the surface shape of the workpiece) How to purchase the machine? Firstly, consider the scale. Own production scale. If the output is not very large, or the output is large but there are many types and the same product is small, it will be more cost-effective to directly polish it by hand. Secondly, care about craftsmanship. Are you clear about the surface treatment process of your own products? Because it involves wiring requirements. The process arrangement is more important. Finally, the quality of employees. If you can't hire the corresponding maintenance and fixture production personnel, you need to consider carefully and don't rush into the horse. At the beginning of the purchase, polishing tests are done on samples.
Valves have a wide variety of specifications, sizes are very different, and there are many types of parts and materials. In addition, the production conditions of each valve factory and the experience and habits of the technicians are different, and the process of compiling valve parts is not consistent. A reasonable process can not only ensure product quality, but also increase labor productivity and reduce product costs. Compiling a reasonable process specification is a relatively complicated task, because in addition to meeting the requirements of product drawings, determining the type of blank, processing methods, and selection of equipment and tooling, it is also necessary to compare and analyze multiple process plans. In addition, whether the preparation of process regulations is reasonable often depends on the technical level and experience of the process personnel. Because the structure, shape and process of valve parts have obvious similarities, the number of valve parts is not large, which is an advantageous condition to realize the typicalization of valve parts process regulations. The typification of the current process is to compile the processing procedures of the other parts into a typical process procedure according to their similar shapes, similar sizes, and the same process. Professional Valve Manufacturing Machines manufacturer here!contact us!
Copyright © 2025 D&S Automatic Co.,Ltd.. All Rights Reserved.
IPv6 network supported