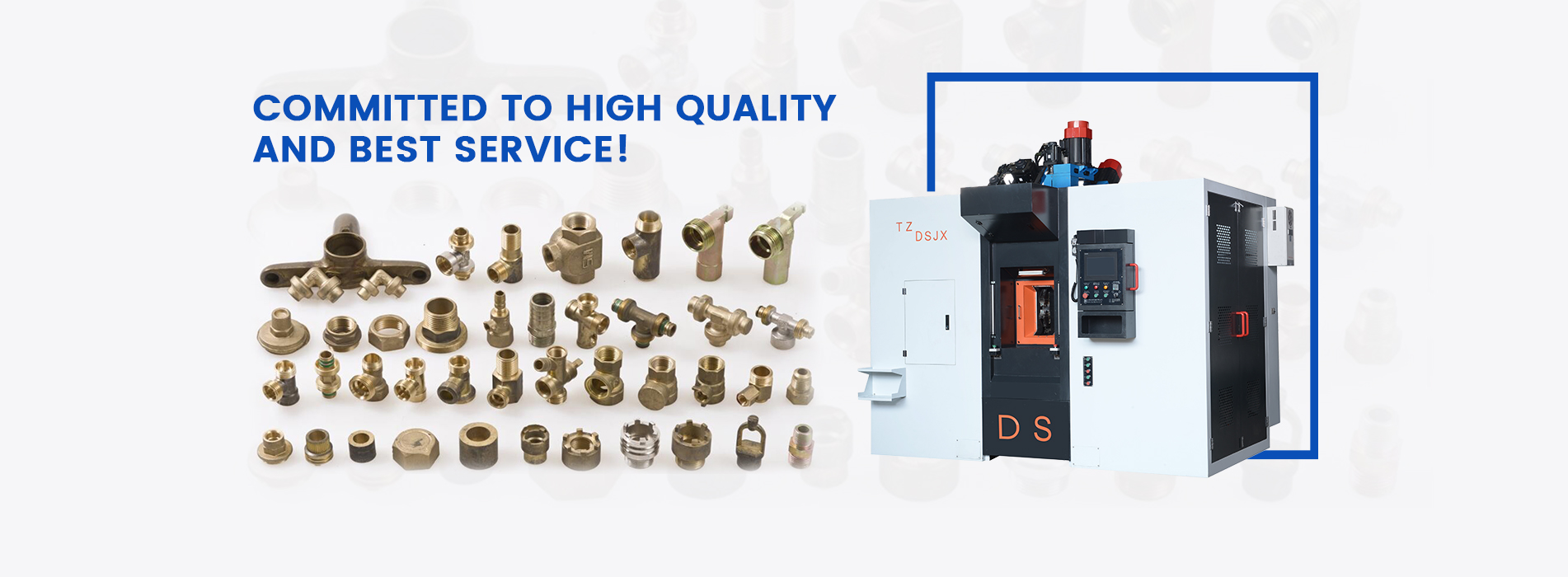
The working principle of an ordinary milling machine.
The main movement of a milling machine is the rotational movement of the milling cutter. On most milling machines (such as vertical lift milling machines), the feed movement is realized by the linear movement of the workpiece in the direction perpendicular to the axis of the milling cutter. Yes, on a few milling machines (such as horizontal lifting table milling machines), the feed motion is the rotary motion or curved motion of the workpiece. In order to adapt to the processing of workpieces of different shapes and sizes, the milling machine has adjustment movements in three mutually perpendicular directions, and can realize feed movement in any one of the directions according to the processing requirements. On a milling machine, the movement of feeding the workpiece and adjusting the relative position of the tool and the workpiece can be realized by the workpiece or by the tool and the workpiece respectively, depending on the type of machine tool. When operating the feed handle of the machine tool workbench, the direction pointed by the handle is the direction of the feed movement of the workbench, making it less likely to cause errors during operation. On the front and left side of the machine tool, there are a set of buttons and handles for the compound operator to operate at different positions. There is a double nut gap adjustment device on the longitudinal wire of the workbench, so it can be used for both reverse milling and down milling. The speed control relay is used for braking, which can quickly stop the spindle rotation. The working principle of a CNC milling machine: On the milling machine, the process, process parameters, and relative displacement of the tool and the workpiece are written into a processing program sheet in CNC language, and then the program is input into the CNC device, and the CNC device will follow the CNC Instructions control various operations of the machine tool and the relative displacement of the tool and the workpiece. When the part processing program ends, the machine tool will automatically stop and process qualified parts. The process can be divided into production process and technological process.
The production process is the entire process of transforming raw materials into finished products. The process is to change the shape, size, relative position and properties of the production object. The process of making it a finished product or semi-finished product. When CNC milling machines process parts, except for manual loading and unloading of workpieces, all processing processes are automatically completed by the machine tool. On the flexible manufacturing system, loading and unloading, detection, diagnosis, tool setting, transmission, scheduling, management, etc. are also automatically performed by the machine tool. Completed. The control information for automatic processing on CNC machine tools is the processing program. When the processing object changes, in addition to changing the tool accordingly and solving the workpiece clamping method, new parts can be automatically processed by simply rewriting and inputting the processing program for the part. There is no need to make any complicated adjustments to the machine tool, which shortens the production preparation cycle and provides a shortcut for the development of new products as well as product improvement and modification. CNC milling machines have a high degree of automation and can complete more surface processing in one clamping, eliminating the need for marking, multiple clampings, inspections, etc.; on the other hand, CNC machine tools have high movement speeds and short idle travel times. short.
Choose D & S Automatic, we will provide you with the best service.
Copyright © 2025 D&S Automatic Co.,Ltd.. All Rights Reserved.
IPv6 network supported